Summary
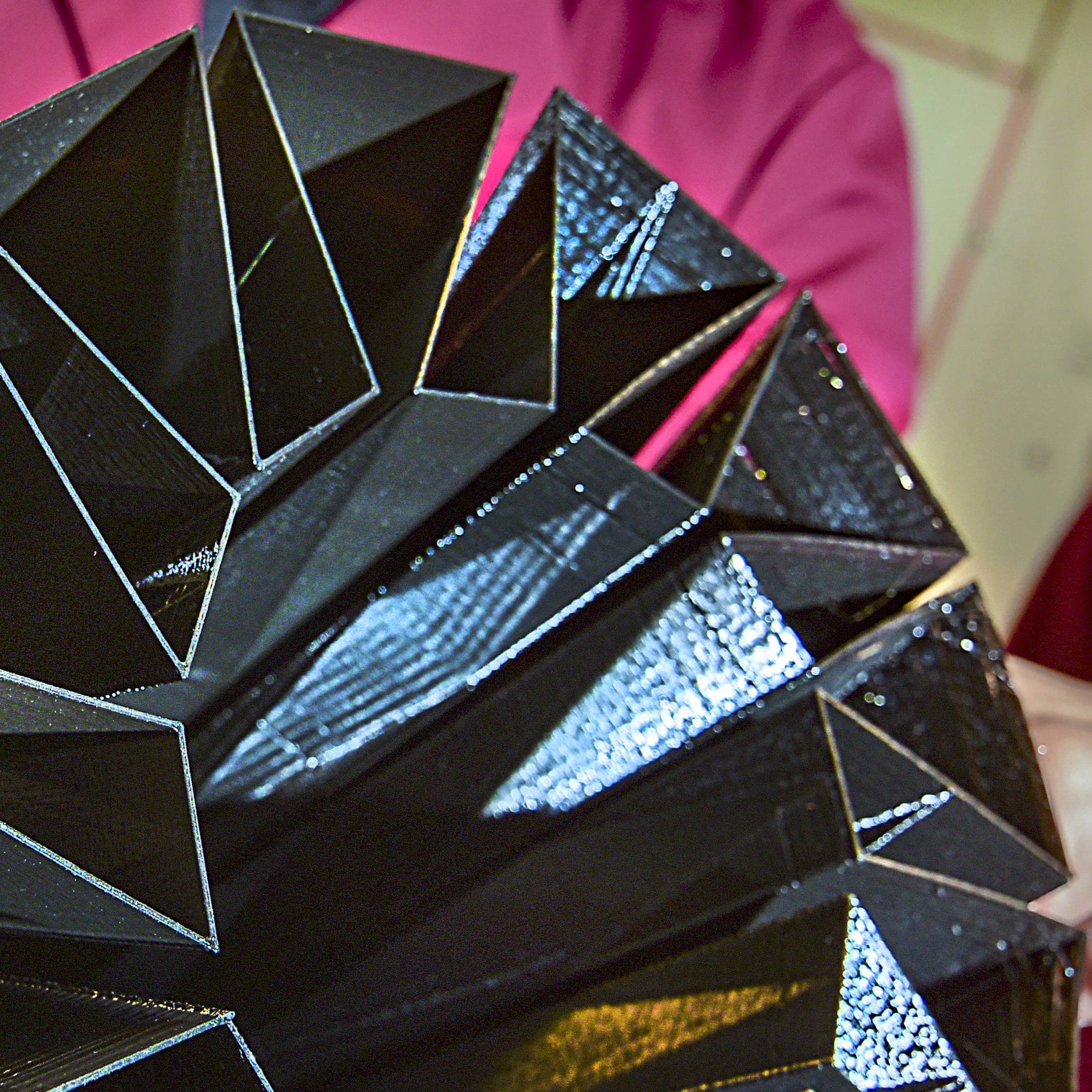
The AIMM (Advanced Infrastructure Materials and Manufacturing) Lab is a cross-disciplinary lab bridging the recent advancements in additive manufacturing and scientific evaluation of the novel manufacturing processes of materials in multiple length scales. We focus on creating new manufacturing and testing-sensing methods of advanced materials developed through various manufacturing techniques including 3D printing, robotics, nanoengineering-nanofabrication, scale-up synthesis, etc. More efficient than conventional construction methods, these new methods can optimize properties, functionalities, performance, and durability of materials for core infrastructure systems and building structures. The AIMM lab is shifting not only how infrastructure is constructed today, but also transforming the way infrastructure is designed and built in the future from beginning to end.
Research
- Development of multifunctional and sustainable construction-building materials.
- Multiscale evaluation of materials and mixtures manufactured via conventional methods, 3D printing, and nanoengineering.
- Development of novel materials and components optimized for additive manufacturing and construction.
- Development of testing, monitoring procedures and smart sensing for improved print quality.
- Development of methods for additive construction, including optimization of process controls.
- Electrochemical sensing, structural materials under extreme environments, and energy storage using nanomaterials including graphene and MXenes.
- Scale-up synthesis and nanofabrication of nanomaterials and graphite from industrial waste stream.
Capabilities
- Multi-axis industrial robotic arm that:
- Development of materials to 3D print large-scale structures for infrastructure applications.
- Delta WASP 4070 3D printer:
- Is capable of printing polymer and clay materials.
- Can print polymers (PLA, ABS, TPU, PETG) filaments via the FDM process.
- Can print cementitious/clay-like materials via the material extrusion process.
- ElectroForce Mechanical Test Instrument (ElectroForce 3330-AT II):
- Mechanical testing system capable of applying dynamic or static mechanical loads (up to 3 kN) to materials for characterization of mechanical properties.
- Dynamic Shear Rheometer (HR30 Discovery Hybrid Rheometer):
- Measuring the viscoelastic properties of materials under oscillatory shear deformation.
- Providing information on rheological behavior such as viscosity, elasticity, and damping characteristics.
- Digital Image Correlation (DIC) System (VIC-3D):
- An optical technique used for measuring full-field displacement and strain fields by tracking patterns on the surface of a specimen subjected to deformation.
- Allied E-Prep Grinder/Polisher (Model 5-2400):
- Smoothing, polishing, and finishing the surfaces of materials to achieve desired surface characteristics via microscopy and nanoindentor.
- Customized Chemical Vapor Deposition System:
- Synthesis of 1D and 2D nanomaterials using controlled chemical reactions with high-temperature furnaces also capable of bulk processing of ceramic materials.
- CELLINK® Bio X6 3D Printer:
- 6 printheads enabling 3D printing of complex structures using soft and biomaterials for nanocomposites.
- X-ARM 7 Robotic Arm:
- A versatile robotic arm with 7 degrees of freedom and a 3.5kg payload capacity.
- Brucker’s Hysitron PI 95 TEM Picoindenter Transducer and Customized MEMS Devices:
- Enables direct-observation nanomechanical testing inside a transmission electron microscope and supports compression, tension, Push-to-Pull, Electrical Push-to-Pull, nanoDynamic, high temperature, and electrical characterization.
- Customized Nanopore Sensing Platform:
- Nanopore sensing using 2D materials with nanometer pore for DNA, bacterial, and virus sensing.
Lab Supervisors:
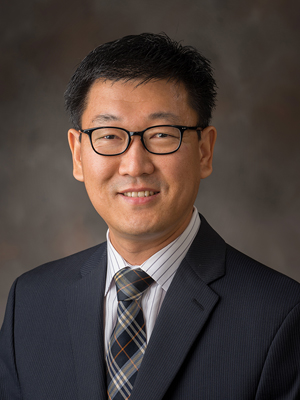
Dr. Yong-Rak Kim
Professor, Zachry Department of Civil & Environmental Engineering
[email protected]
979-847-7366
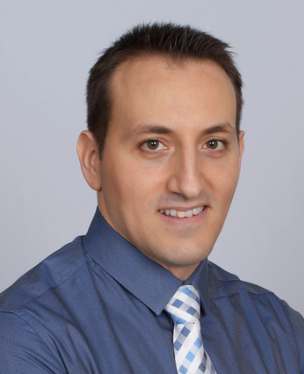
Dr. Petros Sideris
Associate Professor, Civil & Environmental Engineering
[email protected]
979-845-2708